Applications
Pulp & Tissue Additives
Evonik’s process aids, performance additives, wetting agents and defoamer boosters are used to improve water recycling and optimize the efficient use of chemicals and foam control in pulp, paper and tissue production processes.
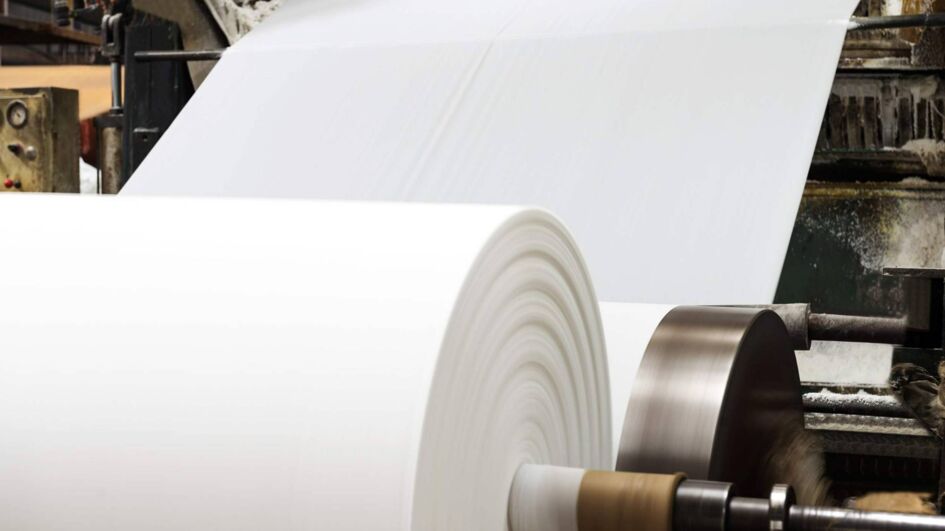
Based on organic specialty surfactants and organomodified siloxanes, our extensive product portfolio covers a variety of product solutions with specific application profiles to address almost all the complex needs of the modern tissue and fluff pulp industry.
Our broad technology solutions for pulp, paper and tissue applications
- Our specialty AROSURF® Softener/Debonder, can be introduced in multiple stages of the of the wet end (headbox, stuff box, or machine chest) process where it imparts increase bulk, improves softness, and antistatic properties for ultimate performance.
- Our AROSURF® lotion concentrate is recommended for the converting process, as it offers ready to use solutions and development of customized solutions for surface fiber finishing.
- Our range of Cooking Additives (e.g., SURFYNOL® and DYNOL ®) improve production and quality of virgin and recycled pulp fibers.
- Our assortment of defoamers and defoamer boosters (e.g., TEGOPREN® and Antifoam®) meets the performance for a broad range of pulp mills that require control of foam production with multifunctional benefits.
- Extend your reach with some of our specialty additives that meet industry standards for food contact compliant with FDA, Bfr, and/or INCI listed for cosmetics ingredients.
Combined with our broad chemical toolbox, our outstanding application and process expertise ensures we can offer our customers the right additive for their formulations. Helping to improve the efficiency of their pulp, paper and tissue production processes.